Technology description
Anaerobic digestion (AD) is a biochemical process in which biogas is produced from organic matter by micro-organisms in the absence of oxygen. The biogas can be produced from bio-waste, waste waters, energy crops and organic by-products from industry and agriculture. Biogas consists mainly of methane and carbon dioxide. (EUBIA 2011)
Anaerobic digestion occurs in a bioreactor, which can be classified as wet and dry reactors. Municipal organic waste and vegetable waste are used in dry reactors, while wet reactors are more commonly used for manure and sludge waste. The operating temperatures are also divided to mesophilic (35 °C) and thermophilic (55 °C) temperatures. The advantage of thermophilic reactors is shorter retention time, but maintaining a higher temperature requires higher energy input. (EUBIA 2011)
The anaerobic digestion process occurs mainly in four steps: hydrolysis, acidogenesis, acetogenesis and methanogenesis. In hydrolysis insoluble organic matter is converted to soluble form. The main idea of acidogenesis is to produce acetate, volatile fatty acids, carbon dioxide and hydrogen. Volatile acids are degraded to acetate and hydrogen by acetogenesis. In the final step, acetate and hydrogen are converted to methane and carbon dioxide by methanogenesis. (EUBIA 2011)
The final product (biogas) can be used for combined heat and power production. The biogas can be also purified to methane and used as a fuel for vehicles. The residues from the anaerobic digestion can provide further benefits as a fertilizer. (MicrE 2011)
Installation of a biogas plan
The design process of a biogas plant starts by defining the properties of raw material s. Raw material can include products from a farm, such as manure, sludge and grass but it also includes external raw material sources. External raw material sources tend to have stricter requirements than raw materials straight from the farm. However, additional payments can be required from external inputs. (Tavitsainen2006)
In cases when there are two or more raw material sources near to each other it may be profitable to build one biogas plant as a joint effort. In this case, the post-treatment of process waste has to be agreed between farmers. Business registration and the amounts of raw materials must be defined and reported. In addition, the use of the raw material can require the permission of a veterinarian. (Tavitsainen2006)
Requirements for an anaerobic digestion process are strongly dependent on biomass feedstock properties. There are no special requirements for a biogas process if it handles only the manure or sludge straight from the farm. External feedstock should be handled properly to guarantee adequate hygiene standards. (Tavitsainen2006)
Raw material may require sterilization as a pre-treatment process. Sterilization kills pathogenic bacteria and, conventionally, this is done by using high temperature in the sterilization chamber. In addition, the sludge that comes out of the bioreactor need to be post-treated by composting, for instance. (Erjava 2009)
One important step is the determination of the computational biogas potential of a biogas plant. Calculation is done by multiplying the annual solid raw material production with the methane productivity potential. (Tavitsainen2006)
Determination of heat and power consumption of the plant is also an essential operation in the beginning. Electricity and heat produced by the plant can be used to run the plant and to heat up households that are nearby. Excess electricity can be transferred to the electric grid and sold to a local electric company. (Tavitsainen2006)
When there is enough background knowledge, the supplier for the process equipment is considered. Some suppliers can perform the energy calculations and preliminary budget offer. In some cases installation costs of a biogas plant can be decreased, if the buyer of a plant helps with construction work. (Tavitsainen2006)
Production of biogas is regulated by several legislation systems related to environment, energy production and agriculture, for instance. At first, the construction permission is needed to build an anaerobic digester. A zoning plan may be useful to check also in the beginning. The supplier and agreement for a biogas plant are also necessary. (Erjava 2009)
Environmental legislation (and waste legislation) is also considered, since the possible environmental damage caused by biogas plant. Environmental legislation might require for instance environmental impact assessment. In addition, collection, storing and transportation of raw material and biogas require separate permissions. For example the requirements for a transportation tank may be strict. Fertilizer legislation is considered in the case when fertilizer is produced by biogas plant and then sold forward. (Erjava 2009)
The installation of a biogas plant usually needs an agreement with a local or regional energy company, especially if the purpose is to sell electricity. Electricity companies can be put out to tender to get good price for electricity, when selling and buying it. (Tavitsainen 2006)
Rescue plan and risk evaluation are also necessary to draft. Also the installation of a biogas plant can be reported to a local rescue authority. Furthermore, the documents related to an ATEX Directive are essential because methane is a highly flammable gas in normal temperature and pressure conditions. (Tavitsainen 2006)
Permissions and legislative systems behind the installation and maintenance of gas pipes also need to be considered, as well as the legislation related to the maintenance of the anaerobic digestion process. Legislative systems and regulations related to biogas plants can vary from country to country substantially. (Tavitsainen 2006)
A checklist for the installation of a biogas plant is presented in Table 1. Compulsory parts are marked with red color, steps to be considered are marked with orange color and discretionary activities are marked with green color.
The ATEX Directive consists of two EU Directives describing what equipment and work environment is allowed in an environment with an explosive atmosphere.
Table 1 Checklist for a biogas plant
Collecting the data |
Define the properties and amounts of the raw material |
|
Computational biogas potential |
|
Determination of heat and power consumption of the plant |
|
Searching a supplier for the process equipment |
Permissions and legislation |
Construction permission |
|
Environmental and waste legislation (EIA) |
|
Fertilizer legislation |
|
Permission to buy and sell electricity with an energy company |
|
Permissions and legislation related to maintenance and running the process, installation on other process equipments (pipes etc.) and transportation, handling and storage of raw material and final products |
Others |
Rescue plan |
|
Documents related to ATEX directive |
|
Risk evaluation |
|
Sterilization process and post-treatment process for the sludge |
|
Permission of a veterinarian |
|
Agreements with other raw material suppliers (responsibilities etc). |
There are always some inhibitors and hazardous compounds related to every process. In the case of a biogas plant, they are highly dependent on the feedstock and the process equipment. The best way to avoid accidents is to follow security instructions and do a preliminary risk evaluation. A rescue plan is also necessary to have. (Tavitsainen 2006)
Biogas consists mainly of methane (CH4) and carbon dioxide (CO2). The desired final product, methane, is a highly flammable gas and it can explode when meeting a spark and reacting with oxygen. Risks can be avoided by designing tanks, reactor and pipes properly to prevent methane leaks. In addition, efficient ventilation is also contributing to preventing the risk of explosion. An alarm instrument detenting high methane concentrations is hence necessary. (Tavitsainen 2006)
Hydrogen sulfide (H2S) is also minor a component of biogas and it possesses flammable, hazardous and toxic properties. The ventilation must work on the floor level because hydrogen sulfide is heavier than air. In a reactor, H2S has also corrosive effects. To prevent the damage of process equipment, H2S is oxidized with 2-5 vol-% air mixture. This is a strict limit for the amount of air because otherwise it would react with methane and cause an explosion. (OSHA 2005, Tavitsainen 2006)
Blockages in the pipes can lead to overpressure, which may cause an uncontrollable discharge. Due to this, homogenous inputs are preferable to heterogeneous inputs. Blockages can occur also in the gas pipes, which are also considered as a safety issue. Special exhaust valve is designed to lead excess gas away controlled manner. (Tavitsainen 2006)
The feedstock, which may include pathogenic bacteria is sterilized. Moreover, the digestate from the reactor is post-treated to fulfill the regulations of the fertilizer legislation. Fertilizer consisting pathogenic bacteria and other inhabitants is not allowed to be used as a fertilizer. Pathogenic bacteria can cause diseases for livestock, for instance. (Tavitsainen 2006)
The feedstock, which may include pathogenic bacteria is sterilized. Moreover, the digestate from the reactor is post-treated to fulfill the regulations of the fertilizer legislation. Fertilizer consisting pathogenic bacteria and other inhabitants is not allowed to be used as a fertilizer. Pathogenic bacteria can cause diseases for livestock, for instance. (Tavitsainen 2006)
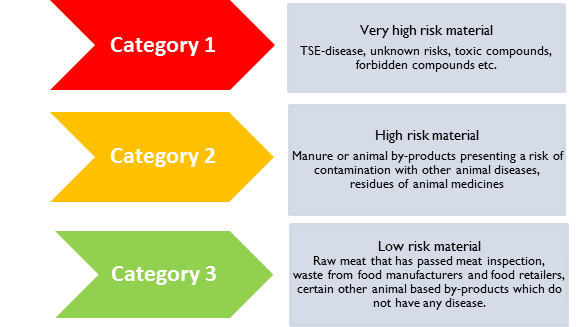
Figure 1 Categorization of animal by-products (Based on Tavitsainen 2006) The categories of animal by-products are illustrated in Figure 1. Feedstock including the material of category 3 is sterilized before further anaerobic digestion to reach adequate hygiene standards. Sterilization is done usually on a temperature of 70 °C for 60 minutes. Sterilization is also done for feedstock including animal-based foodstock and food waste. (Evira 2011)
Thermophilic anaerobic digestion (when temperature is over 50 °C and retention time is at least 20 days) plus composting is an appropriate process combination for the feedstock of category 2. Feedstock related to category 1 is not allowed to be processed by anaerobic digestion. (Evira 2011, Tavitsainen 2006)
There are no special requirements for the anaerobic digestion process if it processing only own manure, milk and washing water from the farm. If the plant is shared with two or more raw material suppliers and the plant processes manure, milk and waste waters from those farms, there are no special requirements for the process. (Tavitsainen 2006)
Treatment of manure from slaughterhouses does not need any special process requirements, except a composting process as a post-treatment. Otherwise the slurry from the process is not allowed to be used as a fertilizer. (Tavitsainen 2006)
If a biogas plant processes only sludge from communities, following processes are appropriate:
- Thermophilic process (55 °C, retention time 4 h)
- Mesophilic process and some of the following alternatives
- Thermal drying (> 80 °C for 10 min)
- Composting and post-maturation (6 months)
- Sterilization (70 °C, 30 min)
Appropriate temperature is essential to maintain due to slow methane fermentation process since product yield decreases immediately when temperature decreases. Adequate retention time and moisture content up to 50 % is a base for productive bio reactor. Moreover pH around 7,5 is optimal for microbial growth and metabolism of these microorganisms. For example if pH exceeds the level of 8, the biogas plant is recommended to be stopped. Formic acid can be added in the case of too high pH. (ECOFYS 2004)
Too high organic load can cause troubles for the process. Recommended amount of organic input varies between 0, 5 – 5 kg per m3. In addition, a healthy carbon to nitrogen ratio should be between 20:1 and 40:1. It is also to be considered that too large particle sizes and lack of auxiliary substances can restrict the microbiological process. (ECOFYS 2004)
Mixing is also needed to avoid pressure build-up and improve the substrate diffusion in the whole reactor. Without mixing, the gas bubbles may not reach the surface, which can cause troubles in the reactor. (ECOFYS 2004)
Feedstock containing antibiotics, disinfectants, heavy metals and organic acids can restrict microbial activity in the reactor or even kill them. If there is electronics default, a professional electrician is needed. The CHP unit can also have malfunctions. In this case, the gas supply from the CHP unit is cut. If there is a gas odor, ventilation is done and sparks and open fire ought to be avoided. (ECOFYS 2004)
Blockages are removed immediately, if the pipes malfunction. If there is malfunction in the pumps, be sure that valves are closed and pumps are switched off. There can be also malfunction in the biogas storage. In this case, the storage is to be ventilated, emptied and the gas supply is stopped. (Tavitsainen 2006)
Sterile process equipment are the base of the process, otherwise it might contaminate by unwanted micro-organisms. Keeping process equipment sterile and preparing with inoculation storage is the best way to avoid contamination. (Vogel 1983)
References
ECOFYS (2004). Planning and Installing Bioenergy Systems : A Guide for Installers, Architects and Engineers.
Earthscan Canada, Toronto. 274 pages. ISBN: 9781849772167. Available at: http://site.ebrary.com/lib/oulu/docDetail.action?docID=10128902&p00=anaerobic%20digestion>
Elintarviketurvallisuusvirasto Evira (2011). [Internet pages].[Cited 15 June 2011]. Available at: http://www.evira.fi/portal/fi/evira/asiakokonaisuudet/
elaimista_saatavat_sivutuotteet/biokaasutus_ja_kompostointi/
Erjava Asmo (2006). Biokaasulaitoksen perustaminen kasvihuonetilalla. Bioenergiakeskuksen julkaisusarja
(BDC publications) Nro 46. 83 pages. Available at: https://publications.theseus.fi/bitstream/handle/10024/20547/ASMO_biokaasu.pdf?sequence=3
European Biomass Industry Association (EUBIA) 2011. [Internet pages]. [Cited 13 June 2011].
Available at: http://www.eubia.org/108.0.html
Micre 2011. [Internet pages]. [Cited 15 June 2011].
Available at: http://nortech.oulu.fi/eng/W2E.html
Taavitsainen Toni 2006. Maatalouden biokaasulaitoksen perustaminen ja turvallisuustarkastelu. Savonia ammattikorkeakoulu (Malla2). ISBN: 952-203-041-4. Available at: http://portal.savonia.fi/img/amk/sisalto/teknologia_ja_ymparisto/
ymparistotekniikka/Malla2Loppuraportti%281%29.pdf
|